Anatomy of Electrical Tape
Vinyl electrical tape is versatile. Its main job is to insulate, but a good tape will form a tight seal that resists corrosive contaminants.
HOW TO CHOOSE VINYL ELECTRICAL TAPE
In vinyl tape selection, there are six key factors to consider: dielectric strength, elasticity, elongation, temperature rating, adhesion and thickness.
CONSIDER THE APPLICATION'S REQUIREMENTS FOR:
The great insulator. An electrician will never use common duct tape as a primary insulator in an electrical installation. Electrical tapes are made with special electrical grade adhesives which don’t contribute to corrosion. The tapes are typically IEC, CSA or UL 510 listed for a voltage rating of 600V, but can go higher with thicker tapes or more layer wraps. Dielectric strength is measured in voltage per thickness. Dielectric withstand is measured in voltage. This is the point beyond which a single layer of tape may show electrical failure. For low voltage applications (<600V), vinyl tape is often the ‘go to’ solution for primary insulation, complex wrapping, abrasion and puncture resistance. For medium voltage applications; rubber, mastic, and molded devices can be used to create the electrical connection insulation. Even when these medium voltage tapes are used for splicing, vinyl electrical tape should be used as outer jacketing. Its tough backing creates a shell and provides excellent resistance to punctures, abrasion and corrosive contaminants.
The vinyl stretch. The capacity for a vinyl tape to stretch is one of the biggest factors in its ability to help protect and seal the installation. Good stretch equals tensile strength. That means pliability and good conformance while making a smooth, uniform and professional wrap. A premium vinyl tape stretches to more than twice its original length—up to 250%—before breaking. The UL minimum requirement for tape stretch is 150%. Premium vinyl tape goes to great lengths to conform, seal, and resist contaminant ingress. And because they stretch so well, they are less likely to break during application which saves time, materials and frustration on the job.
Return to sender. Elasticity is the ability of a material to resume its normal shape after being stretched. The elastic recovery of a vinyl tape describes its ability to efficiently ‘snap back’ to its original length. A tape with excellent elasticity will continue to contract after it’s applied. This is essential to help seal connections from external contaminants. This recovery of the tape provides a better tightening of the tape wraps, forming a seal to resist alkalis, acids and moisture. Premium vinyl tapes have higher elasticity and will stretch and conform better on your connections. Because of this improved recovery, these tapes provide a tightening of the tape wraps, forming a seal to better resist alkalis, acids and moisture. And since they can be stretched and re-stretched multiple times without deforming, during installation you have more time and flexibility to get the job done right without wasting a roll of tape.
Can your tape take the heat and beat the cold? Not all tapes are made to stick in extreme temperatures. Working in cold environments, whether outside braving elements or inside a refrigeration unit, you’ll need a vinyl electrical tape with adhesive that won’t ‘freeze up’ during application. In extreme heat your tape needs a high temperature rating to help prevent peel and material deterioration, both of which compromise dielectric insulation. When evaluating vinyl tapes, the low temperature rating typically provides the lowest installation temperature. The high temperature rating indicates the highest continuous operating temperature of the tape.
Sticky factors. Flagging and tape curl are caused by a number of factors, including adhesive degradation and improper installation. Industrial contaminants and heat can play a factor. Tape can unwind, opening a path for corrosion. Higher grade raw materials are used in the production of premium vinyl electrical tape. Adhesion to steel is part of the ASTM D1000 physical property test for film pressure sensitive adhesive (PSA) tape. It tests how much force is required to pull the tape from a steel surface.
Sword and shield. Electrical insulation can be achieved with tape as thin as paper but to create a shell to help protect from puncture; you need to layer on the vinyl−More specifically: polyvinyl chloride, (PVC). This phenomenal plastic, invented in 1913, is used today in everything from plumbing pipes to credit cards. Early efforts to make a polyvinyl film were stymied by the plasticizer used, which degraded the adhesive. In 1946, 3M researchers created a solution and Scotch® Vinyl Electrical Tape 33 was introduced to the market. Vinyl electrical tapes are often 5 to 7 mil. thick (7 mil is most common in the U.S.). The thinner general purpose tapes are often used for bundling and harnessing cables. Thicker premium vinyl electrical tapes are typically used as primary low voltage insulation. Even thicker 8.5 and 10 mil heavy-duty vinyl electrical tapes will provide extra padding as well as excellent protection in rough environments where your cables and splices are prone to abrasion and punctures. Thickness also plays a part in dielectric strength which increases with each successive wrapped layer. Thicker layers provide increased UV protection for outdoor applications.
Performance Comparisons for Vinyl Electrical Tape
You have a wide array of choices. This easy to read chart will give you performance ratings in a glance.
The case for a jacket
While PVC-backed ‘vinyl’ tapes are the primary insulator in low voltage situations; they are also highly regarded to replace and reinforce cable jackets in low, medium and high voltage applications. Here are many ways vinyl tape helps protect.
Roll with the Pros.
Why do professional electricians prefer premium tape?
Performance
Adhesion • Dielectric • Elongation • Temperature
Premium vinyl electrical tapes have higher values across the key components that impact performance. The stronger the adhesive and the more flexible and conforming the backing, the better the stretch and seal. If the installation is critical, a professional would rather not take risks with their job, their safety or their reputation.
Economy of Use
Critical Jobs • Industrial • Manufacturing • MRO
Electrical installations in an industrial facility require vinyl tapes that stick and stay stuck. If tape doesn’t outlast required maintenance procedures, companies spend more money on unscheduled repairs. Thicker tape creates a stronger jacket and that means greater mechanical protection in rough environments. Premium tape is less prone to flagging. It stretches well to form a tight seal, providing better resistance from corrosive contaminants. Because it has excellent stretch; electricians often use less tape to cover irregular or complex connections, terminations, and bus bars.
Extreme Environments
Hot/Cold • Moisture • Outdoor • Underground
An electrical professional faces harsh conditions on the job. This can mean making splices in freezing conditions. Only premium vinyl tapes can stick quickly in very low temperatures because their adhesive remains soft and sticky. In extreme heat, electricians want to get the job done quickly and efficiently, especially when overwrapping a mastic electrical tape which is engineered to flow when warm. If an economy vinyl tape with low adhesive strength is used in a very hot environment; over time it will curl, become brittle and crack, compromising the electrical insulation.
Peace of Mind
Safety • Reliability • Quality • Reputation
When an installation is hard to get to, like a stadium light, up in the mast of an ocean liner or down in a mineshaft; electricians like to ‘do it right the first time.’ To professionals, it makes sense to use some of the strongest, most durable products. A premium grade tape applied correctly helps reduce the risk of downtime caused by common electrical failures. Premium tapes are engineered for critical applications when you can’t afford to fail.
COMPARE VINYL ELECTRICAL TAPE
PREMIUM VINYL
Highest performance ratings of the Scotch® Vinyl Electrical Tape family. Offering excellent stretch in all weather conditions and increased abrasion resistance. Made in the USA.
- Temperature Range: 0°F to 220°F
- Elongation: 250%
- Adhesion: 28 oz./inch
- UL 510 Listed
- 1” Core, 66 ft. Length
GENERAL PURPOSE
Used for primary insulation up to 600V, harnessing and bundling cable. Medium temperature range and 6 or 7 mil thick. Made in Mexico.
- Temperature Range: -7°C to 90°C
- Elongation: 200%
- Adhesion: 18 oz./inch
- UL 510 Listed
- 1.5” Core, 60 ft. Length
The key to selecting the right electrical tape for your application.
There are some basic rules to follow when you’re selecting electrical tape.
- Vinyl backed tapes have a strong, flexible, abrasion resistant PVC backing which provide a barrier from moisture and corrosive elements. They are often the first and most economical choice for primary and secondary insulation.
- Mastic tapes offer excellent adhesion and sealing characteristics to metals, rubbers, synthetic cable insulations and jackets. They provide UV resistance and are designed for outdoor conditions because they quickly and easily resist moisture.
- Rubber tapes are designed for use in splicing and terminating wires and cables with options rated up to 69kV. They have excellent physical and electrical properties and are ideal for adding moisture protection and padding to electrical connections and cables.
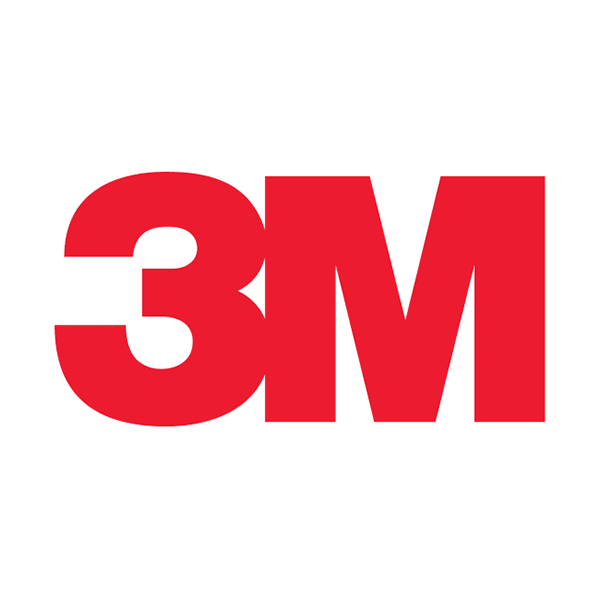
This Resource Compliments of 3M
3M is a global innovation company that never stops inventing. Over the years, their innovations have improved daily life for hundreds of millions of people all over the world. 3M has made driving at night easier, made buildings safer, and made consumer electronics lighter, less energy-intensive and less harmful to the environment. They even helped put a man on the moon. Every day at 3M, one idea always leads to the next, igniting momentum to make progress possible around the world.