Popular Wire Insulation Types
Insulation is a critical component of any wire conducting an electrical current. The right type of wire insulation is determined by numerous factors, including stability, required life, dielectric properties, temperature and moisture resistance, mechanical strength, and flexibility.
Here are the types of wire insulation and why their properties are best suited for different applications.
Selecting the Wire Insulation Type for the Application
There’s no single wire insulation that's ideal for every application. Instead, it's best to look at the requirements of each application and select the wire insulation type that fits best. For example, compressor motors used in refrigerators require wire insulations that can withstand exposure to refrigerants. Additionally, the refrigerator box wires must not impart odors to food and be safe for kitchen use.
Similarly, gasoline pumps require wire that can withstand gasoline vapors. Wire is used in so many different applications that the various types of wire insulation must withstand exposure to liquids, chemicals, temperature changes, and more.
In high-production applications, the process and requirements often dictate the type of wire insulation needed. For example, wire insulation must be solder resistant in some electronic applications using circuit boards. Other applications call for wires capable of encapsulation or wire insulation that can withstand varnish treatment and baking cycles.
The key to successful wire insulation selection is to match the environment and application requirements.
Specifying a Type of Wire Insulation
How do you choose the right wire insulation? Do you know the UL style, the CSA type, or an SAE type? If "YES," those guidelines should answer most of your questions. However, if you need more clarification on the guidelines for the application, then listed below are some simple questions that should get you to the right product.
- What is the approving body? (UL, CSA, CE, SAE, ISO)
- What voltage is required?
- What temperature is required?
- Is plastic okay? Is there limited mechanical abuse? If so, thermoplastic may be a potential solution for your application.
- Need higher durability than plastic? Thermosetting compounds such as EPR, Silicone, and Hypalon offer greater flexibility, higher temperatures, and abrasion. XLP products provide high temperatures, chemical resistance, thin insulation levels, and easy processing. These types of wire insulators are often used for motor lead, panel wiring, and varnish bake cycles.
- What is the application, and how are you using the product?
Exploring Popular Types of Wire Insulation
At the most basic definition, wire insulation covers and holds wires together. It keeps the electrical current contained. Typically, wire insulation is made of different types of plastic or polymers, the two most common types being thermoplastic and thermoset.
So, what are the differences between these two types of wire insulation? Here we break down the compounds and properties of wire insulation.
Thermoplastic vs. Thermosetting Wire Insulation
Thermoplastic:
- Easy to manufacture
- Normally less expensive
- No curing is required
- Will melt when subjected to heat
- It can be extruded in very thin walls
Thermoplastic is a material that will soften, flow, or distort when subjected to sufficient heat and pressure. Thermoplastic compounds are heated and extruded over the conductor. Likewise, the insulation on the finished product can be re-melted or softened if exposed to heat.
Thermosetting:
- Forgiving when exposed to overloads
- Better low-temperature properties
- Higher temperature potential (but will harden and age when overheated)
- Usually more expensive
- Requires a cure process when extruded
- Can not be extruded smaller than 22 AWG in CV processes. Irradiated products can be extruded in smaller sizes.
Thermosetting is a material that will not soften, flow, or distort when subjected to heat and pressure. Once extruded over a conductor, these compounds will not re-melt. However, they can be burnt or deteriorate due to heat.
Thermoplastic Compounds
Thermoplastic compounds use additives to strengthen specific properties of thermoplastic. Depending on the project you are working on, you may want to choose wire insulation that specifically uses one of the following thermoplastic compounds to better serve your needs.
Polyvinyl Chloride (PVC)
PVC is sometimes referred to as vinyl or polyvinyl chloride. This thermoplastic compound consists of three types of vinyl compounds: standard, semi-rigid, and irradiated. The formulation's rated temperature may vary from -55 C to 105 C. Typical dielectric constant values can range from 2.7 to 6.5. PVC is commonly used for the hook up of control wire where the application calls for 1000v or less and 105c and less. It’s also the most economical compound.
Standard PVC
Standard PVC is rated for 1000 volts or less and is used for hook-up, computer, and control wires. Different compounds are used for 60C, 80C, 90C, and 105C service, along with commercial and military applications. Standard PVC is used in building materials like piping, window frames, and electrical cable insulation due to its durability and resistance to environmental factors. It is suitable for the hook up of control wire where the application calls for 1000v or less and 105c and less.
Semi-Rigid PVC (SRPVC)
Semi-Rigid PVC is much tougher than standard vinyl. It has greater resistance to abrasion and cut-through and offers more stable electrical properties. It is commonly used in applications requiring more flexibility than standard PVC, such as thin-wall tubing and flexible cables. Thinner insulation allows this wire to be used in applications that require smaller outside diameter. Insulation is tougher than PVC and offers greater abrasion resistance.
Irradiated PVC
Irradiated PVC wire insulation has improved resistance to abrasion, cut-through, soldering, and solvents. The process of irradiation changes the vinyl from a thermoplastic to a thermosetting material. The material is no longer meltable and is often used where solder is used for connection or termination. Its enhanced resistance to chemicals, abrasion, and heat makes it suitable for aerospace and automotive cable insulation.Â
Polyethylene (PE)
Polyethylene, or PE, is very good wire insulation as it offers a low dielectric constant, a stable dielectric constant over all frequencies, and a very high insulation resistance. In terms of flexibility, Polyethylene can range from stiff to very hard depending on molecular weight and density. The low density is the most flexible, while high density and high molecular weight formulations are very hard. Moisture resistance is excellent. However, both types are flammable. Brown and Black formulations have excellent weather resistance. The dielectric constant is 2.3 for solid insulation and 1.5 for cellular (foamed) designs.
Rulon
Rulon is a flame-retardant polyethylene that contains additives to inhibit the rate of burning. These additives have only a slight effect on the physical or electrical properties of the insulation. It is known for its low friction and excellent resistance to chemicals; used in gaskets, slide bearings, and non-stick surfaces.
Propylene (Solid and Cellular)
Propylene is similar in electrical properties to Polyethylene. This material is primarily used as wire insulation. Typically, it is harder than Polyethylene, making it suitable for thin wall insulations. UL maximum temperature ratings may be 60C or 105C. The dielectric constant is 2.59 for solid and 1.55 for cellular (foamed) designs. It is used in automotive interiors, food containers, and medical devices due to its fatigue resistance, low cost, and chemical resistance.
Kynar
Kynar has excellent mechanical strength, superior resistance to abrasion and cut-through, and substantially reduced cold flow, which makes it a superb backplane wire insulation. In addition, Kynar is self-extinguishing, radiant-resistant, and rated at 135C. It is used in chemical piping systems, wire coatings for nuclear plants, and as a protective coating in chemical applications.
Tefzel (ETFE)
Tefzel wire insulation is rated at 150C and has very good electrical properties, chemical inertness, high flex life, and exceptional impact strength. Tefzel can withstand an unusual amount of physical abuse and is self-extinguishing. Tefzel is a registered trademark of DuPont Corporation. It is commonly used in applications requiring high corrosion resistance and strength over a wide temperature range, such as architectural films and aerospace wiring.
Halar (ECTFE)
Halar wire insulation has a specific gravity of 1.68, the lowest of any fluorocarbon. Its dielectric constant and dissipation factor at 1 MHz are 2.6 and 0.013, respectively. Halar chars but does not melt or burn when exposed to direct flame and immediately extinguishes on flame removal. Its other electrical, mechanical, thermal, and chemical properties are almost identical to Tefzel's. Its temperature rating is -70C to 150C. Halar is a registered trademark of Solvay.
Teflon (FEP)
Teflon insulation is extrudable like PVC and Polyethylene, allowing for long wire and cable lengths. FEP has excellent electrical characteristics, chemical inertness, and a service temperature of 200C. Teflon is a registered trademark of Chemours.
Teflon (TFE)
Teflon TFE is extrudable in a hydraulic ram-type process. Lengths are limited due to the amount of material in the ram, insulation thickness, and preform size. TFE wire insulation must be extruded over a silver or nickel-coated wire, with ratings at 260C and 200C, respectively. Teflon is a registered trademark of Chemours. TFE and PFA are more expensive than PVC compounds (8-10X), but offer greater electrical characteristics and higher operating temperatures (200-260c). They are also resistant to virtually all chemicals as well as flame resistant.
Teflon (PFA)
PFA is the latest addition to Teflon resins. Like the others, it has outstanding electrical properties, high operating temperature (250 C), resistance to virtually all chemicals, and flame resistance. PFA is a registered trademark of Chemours.
Thermoplastic Rubber (TPR)
Thermoplastic Rubber, or TPR, has properties like those of vulcanized (thermosetting) rubbers. The advantage is that, when processed like thermoplastics, it is extruded over the conductor. Like many conventional rubber materials, TPR is highly resistant to oils, chemicals, ozone, and other environmental factors. In addition, it has low water absorption and excellent electrical properties and is very flexible with good abrasion resistance.
Thermoset Compounds
Thermoset compounds are often used in applications that include higher temperatures because they don’t melt when exposed to heat. They also maintain their shape better in colder environments. Commonly used types of Thermosets include the following.
Chlorosulfonated Polyethylene (CSPE)
CSPE is sometimes used as a 105C-rated motor lead wire insulation but most often as a jacketing compound. CSPE has excellent tear and impact strength, abrasion, ozone resistance, oil and chemical resistance, and good weathering properties. This material also has low moisture absorption, excellent resistance to flame and heat, and good dielectric properties. This can be applied in automotive and marine upholstery, hoses, and cable jackets.
Silicone
Silicone is a soft insulation with a typical temperature range from -80C to 250C. It has excellent electrical properties, ozone resistance, low moisture absorption, weather resistance, and radiation resistance. However, silicone typically has low mechanical strength and poor scuff resistance. While silicone rubber burns slowly, it forms non-conductive ash, which, in some cases, can maintain the integrity of the electrical circuit. It is often used in commercial cooking equipment, medical equipment, and other high temperature applications. It is often used in marine, motor, power and mining applications.
Ethylene Propylene Rubber (EPR)
EPR is a chemically cross-linked, thermosetting high-temperature rubber insulation. It has excellent electrical properties combined with outstanding thermal stability and flexibility. EPR's resistance to compression, cutting, impact, tearing, and abrasion is good. Acids, alkalis, and many organic solvents don't impact this thermoset wire insulation. It is also highly moisture resistant. EPR has temperature ratings up to 150C.
Cross-linked Polyethylene (XLP)
Cross-linked Polyethylene (XLP) is a wire-insulating material with more robust resistance to environmental stress cracking, cut-through, ozone, solvents, and soldering than either low- or high-density Polyethylene. It is sometimes designated as XLPE. It can be cross-linked either chemically or irradiated.
Semi-Butyl Rubber (SBR)
SBR is flexible and offers good heat and moisture resistance at an economical cost. The wire must still be jacketed for mechanical and chemical protection. SBR is suitable for 75C max temperature ratings.
Importance of Choosing the Right Type of Insulation
Selecting the appropriate insulation type for electrical applications is critical due to its impact on safety, efficiency, and compliance. Many factors play into choosing wire and cable, including the type of wire insulation suited to your specific application. Explore the links below to learn more. Search our wire and cable products catalog to find the right solution for your next product or project. Explore the links below to learn more. Search our wire and cable products catalog to find the right solution for your next product or project.
Learn more about wire insulation from these related resources:
- Popular Jacket Types: explore the different types of wire jacket materials and compounds.
- Tape Types: understand the different options and properties of tape insulation.
- Properties of Common Thermoplastic and Thermoset Compounds: this matrix shows the properties of thermoplastic and thermosets.
- Low Smoke Zero Halogen Compounds: learn about LSZH behavior when combusted and the toxicity of emissions.
Need support in finding the right insulation for your application?
Contact IEWC to connect with a member of our team!
Related Resources
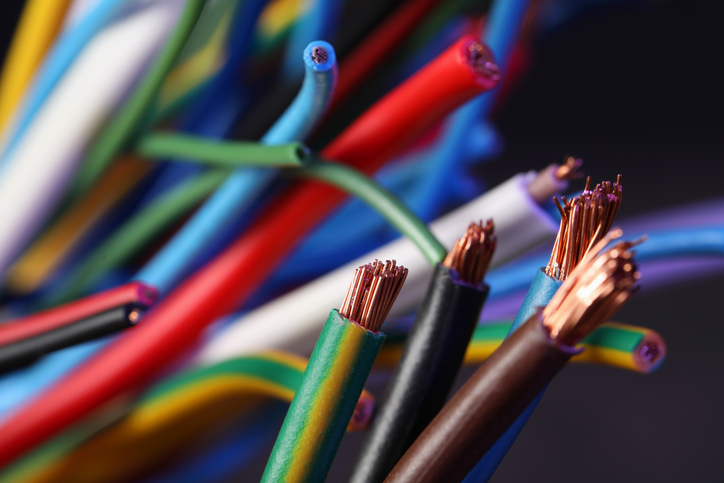
Popular Jacket Types
Jackets cover and protect the enclosed wire or core against damage, chemical attack, fire and other harmful elements which may be present in the operating environment. Learn More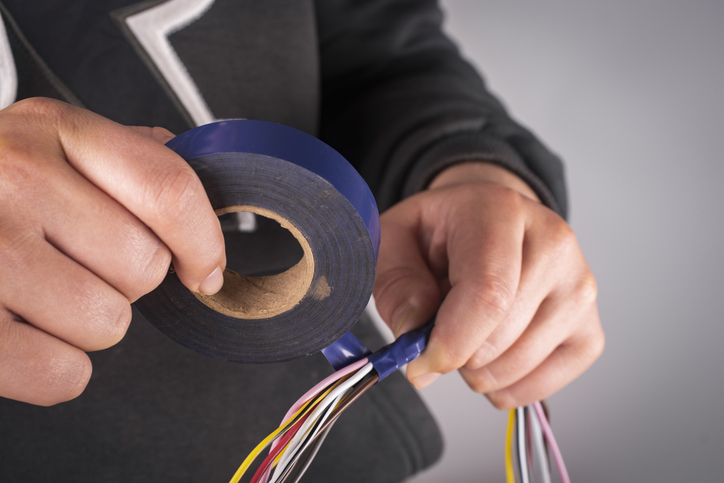
Tape Types
Tape insulations play a crucial role in providing electrical insulation , particularly in scenarios where other materials might fall short.Learn More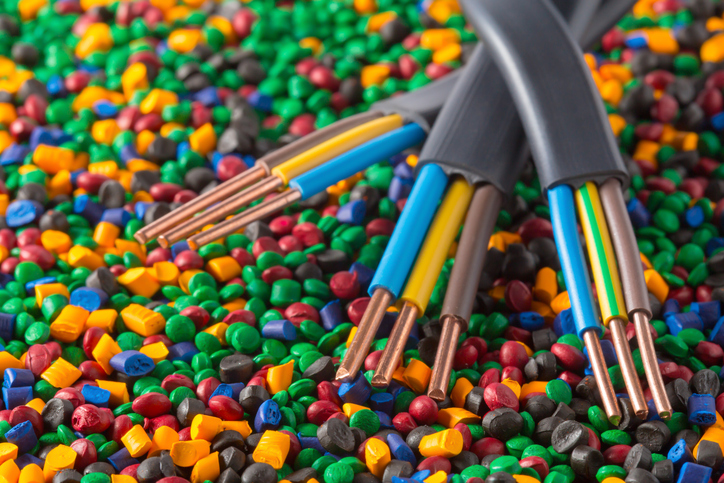
Properties of Common Thermoplastic and Thermoset Compounds
Thermoplastic and Thermoset compounds are types of polymers with different melting points and tensile strength.Learn More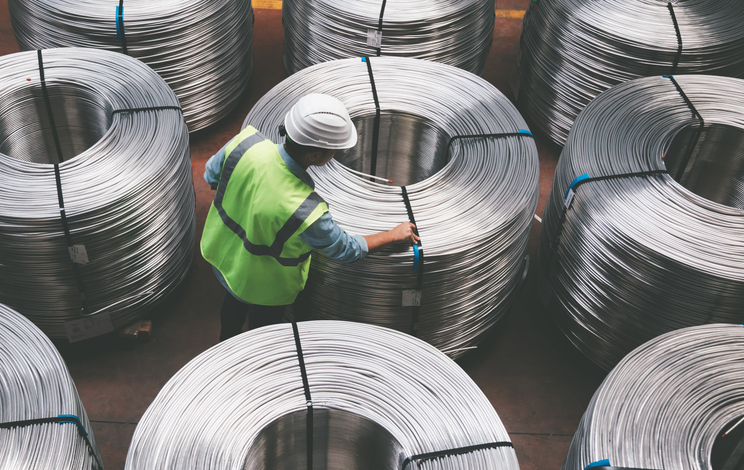