Power Distribution System Design for Industrial Environments
Industrial environments require power. A reliable power distribution system ensures that the heavy machinery, lighting, and control systems work without interruption. Electrical systems require special planning and diligence.Â
Of course, in any industrial environment, efficiency is mandatory, and safety is paramount. Without a properly designed power distribution system, you could risk downtime, higher operating costs, and potential safety hazards that could disrupt production (or put staff in danger). Here, we'll explain what you need to know to assess your power needs, choose the right cable, and meet those critical safety standards.
Assessing Your Power Needs
How do you assess your facility's power distribution needs? You need to determine the current and future energy demands. Look at the power you need today and what you will need to accommodate growth in the future. By carefully preparing, you'll ensure that you have smooth, safe operations that help you avoid accidents and downtime. You may need to engage electrical engineers and experts to ensure you meet industry standards for your industrial power distribution system.
Understanding Your Current Power Demand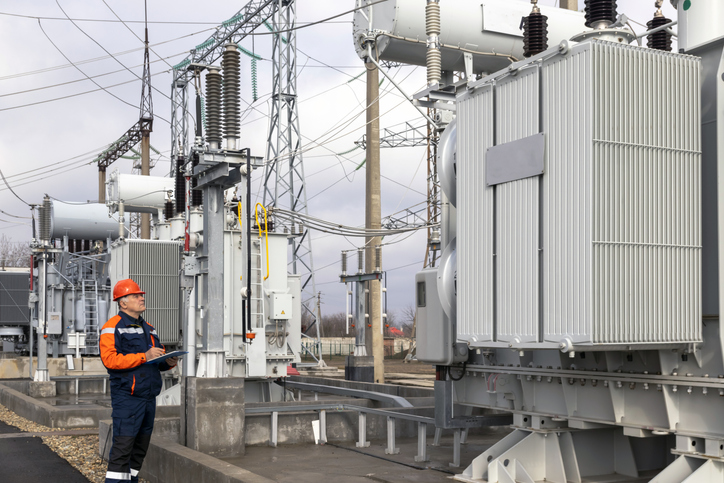
Your first step in designing your power distribution system is evaluating the facility’s current energy requirements, including the energy consumption of equipment, machinery, and operations.
Look at the power demand during peak usage or the most critical use period. Calculate out the peak loads as well as the average loads—this will help you make sure that your system can not only handle the times of maximum energy consumption but also remain efficient even during periods when the load is lighter.
Calculating Peak and Average Power Loads
To calculate the power loads of your equipment, you'll want to list all the equipment in your facility and the power ratings (in either kilowatts or amps). Then, choose different times of the day—peak operations and lulls to monitor your power usage.
You can use this data to figure out your peak load (the maximum power used by your operations simultaneously) and the average load (overall energy consumption over a set period of time).
Planning for the Future
Your next step is to look ahead. Chances are high that your operations will expand and grow in the future. Industrial facilities may need to add new equipment, change or increase production, or perform new operations. Your power system must be able to accommodate the higher voltage levels of that growth, or you'll be subject to costly updates, redesigns, or overloads that lead to downtime.
How do you anticipate the future power usage of your operation? Carefully look at your 5-10 year plan. What is the expected increase in equipment selection or production? Obviously, it won't be an exact calculation, but you can use trends to make an educated prediction.
The power system you design should include the extra capacity for growth. You need to be sure that switchgear, cabling, and transformers can stand up to figure demands without fail. The best practices are to create a modular system that can be easily adjusted.
Load Balancing and Efficiency
What is load balancing? When we talk about an electrical power distribution system and load balancing, it refers to distributing the electrical load evenly across the system or circuit. Load balancing prevents system overload and strain on your electrical network.
So, how do you achieve a balanced load? You'll want to divide your space into zones or sections. Each zone is then assigned a dedicated power source. You should distribute your most power-intensive equipment across the different zones or circuits.
Load balancing works alongside energy-efficient practices to reduce the strain on your facility. You should regularly monitor each zone to make sure that nothing is overloaded or under strain. You can further reduce your energy consumption by choosing energy-efficient equipment, reducing energy use during non-peak hours, and following production schedules.
Choosing the Right Cable for Your System
The right cable is critical for safe, efficient, and reliable operation. With the wrong cable, your facility may experience more breakdowns and downtime, require more maintenance, and even face safety hazards.
The cables you choose should always match the voltage and current. You also need to consider the facility's environmental conditions.
Assessing Voltage and Current Requirements
Each part of your system may need a different type of cable in order to handle specific voltage and current requirements. To find the voltage and current needs, you’ll want to identify the voltage level required in each section of your industrial power system.
Keep in mind, most industrial power systems rely on high voltage, which will require specific types of cables. It's crucial that your system can handle changes in the input of the load and accommodate fluctuations and spikes. This is typically done with the use of regulators, filters, capacitors, transformers, or feedback loops.
You'll then calculate the current load by adding up the amperage required by all your connected equipment. Your cable will need to have the right ampacity (the maximum amount of electrical current a cable can carry) for your regular operating conditions as well as peak loads. It's better to overestimate the capacity slightly so you know your cable will keep up with any demand.
Choosing the Right Cables
Once you’ve determined your ampacity and voltage requirements, you’ll refer to cable selection charts to find the best cable type. Need assistance? IEWC is here to help. Reach out to our team with any questions or concerns.
You'll want to ensure that the cables you've selected meet the NEC voltage and current capacity standards.
When selecting industrial cable, you’ll need to consider the operating environment that the cables will face. Industrial environments can be tough—cables may be exposed to moisture, chemicals, temperature fluctuations, abrasion, and mechanical stress.
Your application requirements will help you determine what you need for insulation and sheathing to protect your cable from environmental challenges. The main factors to explore are:
- Temperature: Choose a cable that can withstand the highest and lowest temperatures the environment presents.
- Moisture: Moisture causes corrosion and short-circuiting. The cable you choose for humid and wet environments, but include water-resistant or waterproof insulation.
- Chemical Exposure: Chemicals and solvents can degrade cable over time. Depending on the chemical exposure, you’ll need to select cable with appropriately resistant material.
- Mechanical Stress: Over the course of their job, cables might get bent or crushed. They could experience high levels of abrasion. Be aware of these challenges and select extra reinforcement like armored sheathing.
Materials like XLPE (cross-linked polyethylene) insulation and TPU (thermoplastic polyurethane) offer temperature, chemical resistance, and mechanical durability. It's important to consider all the hazards your cables may face over the course of their job and in the most extreme conditions.
You’ll also want to consider the durability of the cables you select. When you design a power distribution system, you need cables that can stand up for the long haul. To assess durability, check the manufacturer's ratings for tensile strength, temperature, and abrasion resistance. Cables will also have a lifespan estimate.
Cables are tested for environmental degradation under conditions like exposure to UV light, moisture, and mechanical wear and tear. Choose cables that meet the standards of your environment so you're assured of a long lifespan and optimal performance.
Safety Standards and Compliance
In industrial applications, safety is everything. When designing power systems, it's crucial that you meet all safety regulations and standards, so your equipment runs smoothly and your team is protected from any electrical dangers and hazards.
Critical Regulations for Industrial Power Distribution
There are several important regulations that govern the design and installation of power distribution systems for industrial use. The most widely used and recognized standards are:
- The National Electrical Code (NEC)
- International Electrotechnical Commission (IEC)
- Occupational Safety and Health Administration (OSHA)
Complying with these crucial standards will impact your power system designs and plans. For example, OSHA regulations may require that you follow lockout procedures during maintenance. The NEC guidelines may dictate your cable selection based on voltage and insulation requirements.
Staying compliant with all electrical code requirements and regulations is essential to ensure reliable operation. Regularly review local, national, and international regulations to ensure your team stays up-to-date on the latest rules, guidelines, and safety measures.
When designing and installing power distribution systems, it's important to enlist the help of certified professionals. It's also crucial that you use appropriately rated equipment and components.
Maintain documentation of your system, installation procedures, and design diagrams and materials so that you're able to easily inspect the system and perform maintenance as necessary. Regular audits and safety inspections should be a part of your standard operating procedures. Check the grounding and insulation intensity and monitor the overall system performance. Note and address any changes or concerns immediately.
Essential safety measures include:
- System Grounding & Bonding systems: To prevent shock hazards and electromagnetic interference from stray electrical equipment. Use connectors, wires, ground rods, or electrodes.
- Circuit Breanders & Fuses: These protect equipment from short-circuiting—when a current goes through the wrong path and damages your system. Short circuits can be dangerous to your entire electric power distribution system. Fuses, relays, current limiters, and circuit breakers are all part of circuit protection.
- Fire Safety Measures: Your cable systems must use fire-resistant materials and proper routing. Certain higher-risk environments may require flame-retardant cables and conduits. Fire suppression systems should be strategically set up near electrical equipment.
- Harmonic Mitigation: Harmonics are current anomalies caused by nonlinear loads (such as inverters or switching devices). You must avoid harmonics to ensure your system is efficient and safe. You can use reactors, transformers, filters, and harmonic compensators to do this.
When designing a power distribution system for your industrial facility, the biggest focus should be on safety, regulator compliance, performance, and efficiency. It all comes down to good design and making sure you always have the suitable cable for the job.
At IEWC, we carry a vast range of cables and components to meet your system requirements. If you need assistance navigating your selections, please reach out to our team. We’re happy to help you find the best cable for your industrial power system design.
Related Resources
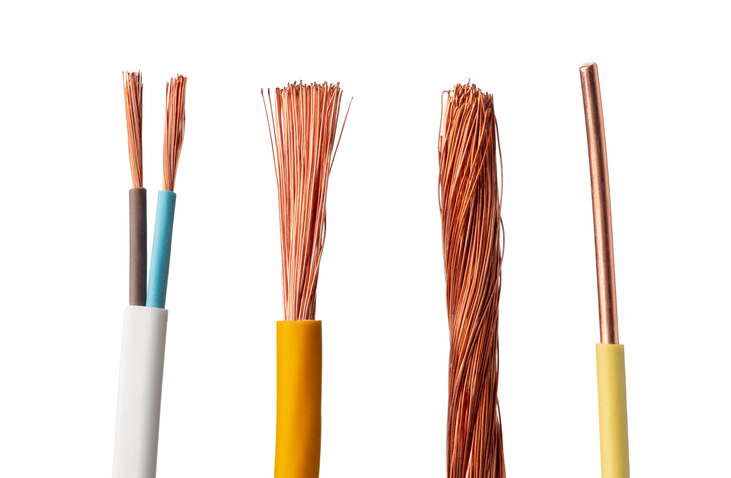
What is a Wire?
Wire refers to a single, usually cylindrical, strand or rod of metal which is used to carry electricity and telecommunications signals. Learn More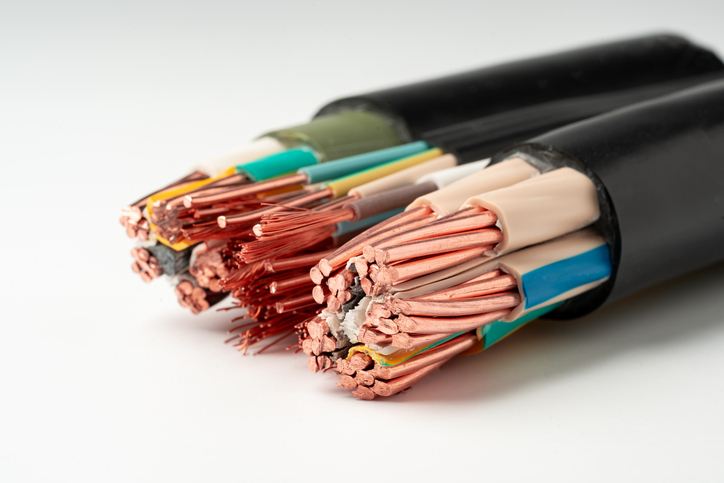
What is a Cable?
Cable, or cabling, consists of the twisting together of two or more insulated conductors.Learn More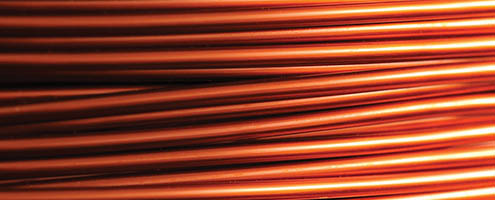
Selecting a Conductor
Even in the design of a simple single insulated wire many factors must be considered, including physical properties of the conductorLearn More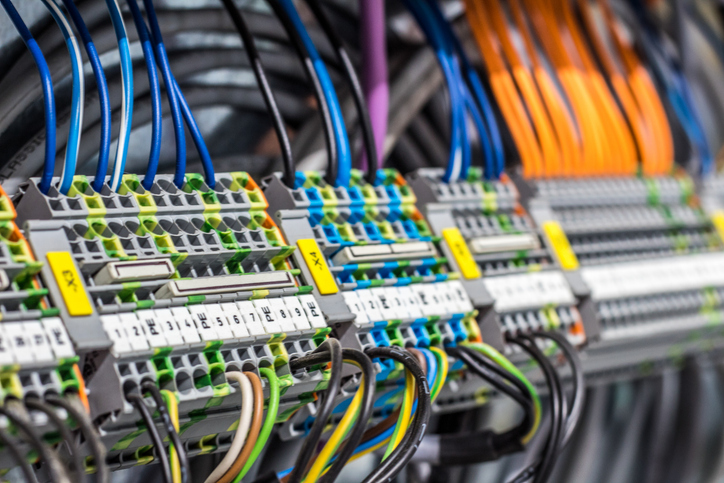