Selecting a Conductor
How to Select the Right Conductor for Your Application
When designing even the simplest insulated wire, several critical factors must be taken into account. These include temperature tolerance, voltage rating, DC resistance, insulation properties, overall diameter, required flexibility, and the physical characteristics of the conductor such as tensile strength, voltage drop, conductivity, and weight. Additionally, specific electrical attributes like the dielectric properties of the insulating material may also be necessary.
Key Factors in Choosing an Insulated Conductor
Selecting the appropriate insulated conductor involves careful consideration of multiple factors, particularly those related to the conductor’s size, stranding, and material composition.
Understanding Conductor Size
Conductor Size: The size of a conductor is crucial and is primarily determined by its DC resistance, current-carrying capacity, and breaking strength requirements.
Gauge: In the U.S. and Canada, the American Wire Gauge (AWG) system is used to specify wire sizes. An important aspect of calculating the appropriate AWG size is ensuring that the Circular Mil Area (CMA) meets the standards set by organizations like ASTM (American Society for Testing and Materials), UL, CSA, and SAE. As the gauge number increases, the wire diameter decreases.
Circular Mil Area (CMA): Size can also be expressed using Circular Mil Area, which is an arithmetic shortcut to determine the cross-sectional area of a round wire. For example, 500 MCM (thousand circular mils) is equivalent to 133 strands of individual wires with a total of approximately 500,000 circular mils.
Metric Conversion: For reference, the metric equivalents of AWG sizes range from 0.08 mm² for 28 AWG to 500 mm² for 1000 MCM.
Metric Equivalent Of AWG
AWG | mm2 |
---|---|
28 | 0.08 |
26 | 0.14 |
24 | 0.25 |
22 | 0.34 |
21 | 0.38 |
20 | 0.50 |
18 | 0.75 |
17 | 1.0 |
16 | 1.5 |
12 | 4.0 |
10 | 6.0 |
8 | 10 |
6 | 16 |
4 | 25 |
2 | 35 |
1 | 50 |
1/0 | 55 |
2/0 | 70 |
4/0 | 120 |
300MCM | 150 |
350MCM | 185 |
500MCM | 240 |
600MCM | 300 |
750MCM | 400 |
1000MCM | 500 |
Exploring Conductor Stranding
Stranded Conductors: Stranded conductors are developed to address the rigidity of solid conductors. They consist of smaller gauge wires bundled or wrapped together to form a larger conductor. The gauge size of stranded conductors is often represented by the overall size combined with the size of each individual strand. For instance, a 16 AWG 26/30 conductor has 26 strands of 30-gauge wire.
Advantages of Stranded Conductors:
- Enhanced Flexibility: Stranded conductors offer greater flexibility, making them easier to install in various applications.
- Extended Flex Life: These conductors can withstand more vibration and bending without breaking, providing a longer lifespan compared to solid conductors.
- Reduced Surface Damage: Any damage, such as scratching or nicking, is less severe in stranded conductors compared to solid wires.
- Strand Count Impact: The number of strands in a conductor affects its flexibility and cost. More strands typically mean greater flexibility but also higher costs.
Selecting the Right Conductor Material
Copper: Copper, either bare or tinned, is the most commonly used material for conductors due to its excellent conductivity, ductility, and thermal properties.
Aluminum: Aluminum is another option, offering similar properties to copper, such as ductility and malleability. However, it has only 61% of the conductivity of copper, requiring larger wire diameters to achieve the same current-carrying capacity. Aluminum is less commonly used in OEM applications due to its limitations, including reduced flex life, difficulty in soldering, and potential for corrosion when in contact with other metals.
Bronze or Copper-Coated Steel: These materials are used in applications requiring high tensile strength, such as coaxial cables or specialized cords.
High-Strength Alloys: When both strength and flexibility are paramount, high-strength copper alloys such as cadmium-chromium copper, cadmium copper, and chromium copper are preferred. Although more expensive, these alloys allow for significant size and weight reductions while maintaining high breaking strength and greater flex life.
Selecting the right conductor involves understanding the interplay between conductor size, stranding, and material. By considering these factors, you can ensure that your wire and cable applications meet the necessary performance requirements, whether for everyday use or specialized industrial needs.
Related Resources
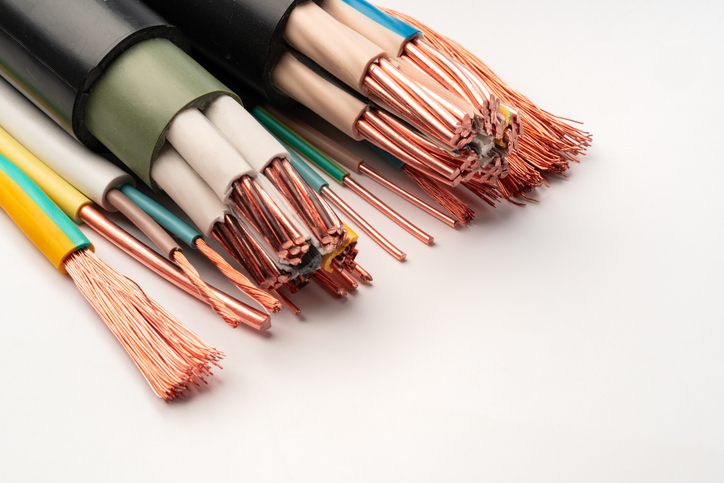
Basic Ampacity Values
Ampacity, or current carrying capacity, is defined as the current a conductor can carry before its temperature rise exceeds a permissible value.Learn More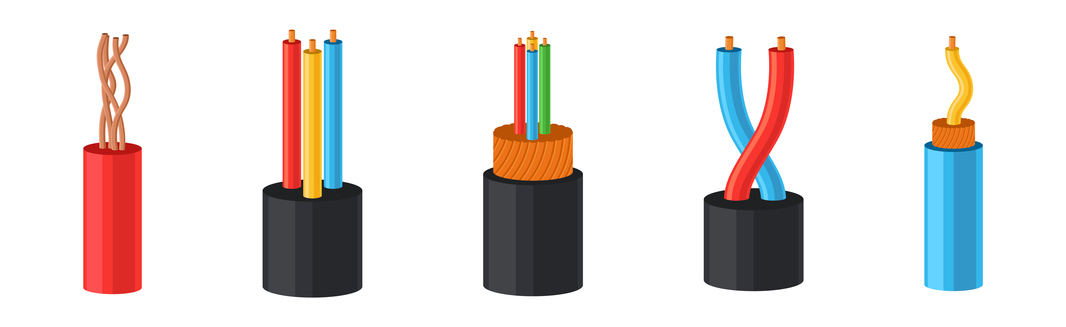
Types of Strand Construction
Strand construction in wire and cable is crucial because it directly affects flexibility, durability, and electrical performance, impacting the overall reliability and efficiency of the cable in various applications.Learn More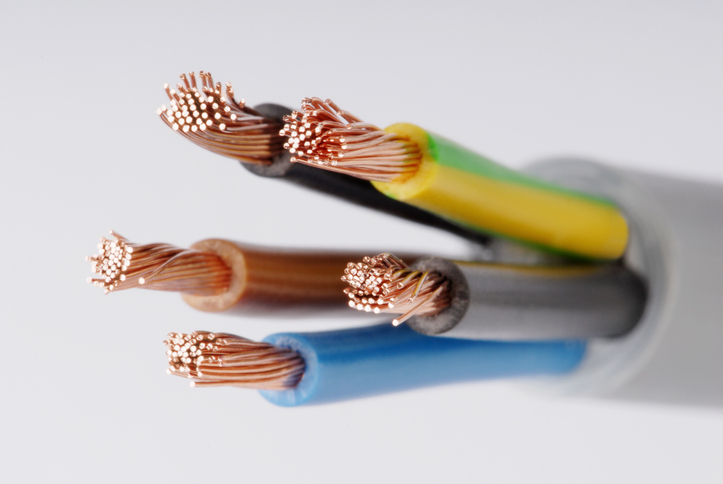
UL, Metric & SAE Strand Charts
Discover additional information on UL, Metric and SAE Strand ChartsLearn More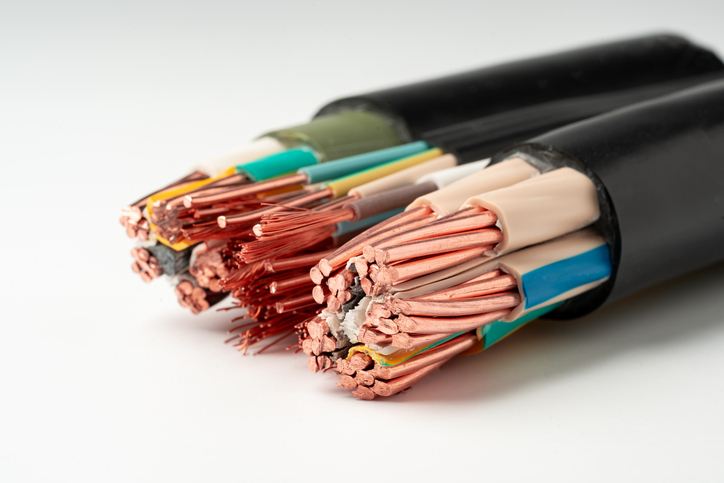