Jacket Selection
The Importance and Specification of Cable Jackets
Cable jackets, also known as sheaths, serve a crucial role in safeguarding the internal components of a cable. They enhance the cable's appearance while providing essential protection against flames, mechanical stress, thermal conditions, chemicals, and environmental factors. The selection of a proper jacket is vital for ensuring the longevity and reliability of the cable in its intended application.
The Functionality of Cable Jackets
Cable jackets are not merely for aesthetic purposes; they are designed to protect the delicate internal structures of the cable, including the conductors and insulation. These jackets are engineered to withstand various hazards, such as high temperatures, harsh chemicals, physical abrasions, and environmental conditions. By shielding the cable from such risks, the jacket ensures that the cable performs optimally throughout its service life.
Many jackets are made from extruded insulation materials, though some compounds are specifically formulated for jacketing purposes. Often, manufacturers use a combination of compounds, layered together, to create jackets that offer enhanced protection. Common materials used for cable jackets include thermoplastics and thermosetting compounds such as polyvinyl chloride (PVC), polyethylene, neoprene, chlorinated polyethylene (CPE), thermoplastic rubber (TPR), chlorosulfonated polyethylene (CSPE), polyurethane, fluorocarbons, Hypalon, Halar, fluorinated ethylene propylene (FEP), polytetrafluoroethylene (PTFE), Tefzel, ethylene propylene rubber (EPR), and silicones.
Key Considerations When Specifying a Cable Jacket
Selecting the appropriate cable jacket requires careful consideration of several factors. Here are the critical questions to guide you in specifying the right jacket for your application:
1) What is the Approving Body?
The first step in selecting a cable jacket is determining the relevant approving body, such as UL (Underwriters Laboratories), CSA (Canadian Standards Association), CE (Conformité Européenne), SAE (Society of Automotive Engineers), or ISO (International Organization for Standardization). If your cable needs to meet a specific standard from one of these bodies, it will significantly influence the type of jacket you should choose.
2) What is the Application Environment?
Understanding the environment in which the cable will operate is crucial. Will the cable be exposed to abrasive conditions, chemicals, oils, or require constant flexing? Different environments demand different types of jackets. For instance, cables exposed to chemical environments may require a jacket made from a material with high chemical resistance, such as Tefzel or fluorocarbons.
3) What Voltage Will the Cable Carry?
The voltage rating of the cable is another critical factor. For most OEM (Original Equipment Manufacturer) applications, 150, 300, and 600 volts are common. However, MRO (Maintenance, Repair, and Operations) applications may require cables rated from 1000 volts up to 35KV. The cable jacket must be capable of withstanding the electrical demands of the application without compromising safety or performance.
4) What Temperature Range is Required?
Temperature is a key consideration in jacket selection. Most cable jackets are rated for temperatures up to 105°C. For applications requiring higher or lower temperature resistance, specific materials are necessary. For instance, silicone, Halar, FEP, PTFE, and TPR are known for their ability to perform well in low-temperature environments, with some materials functioning effectively at temperatures as low as -55°C to -65°C.
5) Is Cost a Major Concern?
Budget constraints often play a significant role in the selection process. Generally, thermoplastic materials are more cost-effective compared to thermosetting materials. However, the long-term benefits of choosing a more expensive material, such as extended cable life or reduced maintenance costs, should also be considered.
6) What Color is Required?
The color of the cable jacket is not merely for aesthetics; it can serve practical purposes such as identification and safety. Black and grey are the most commonly used colors for cable jackets, but specific applications may require different colors to distinguish between cable types or functions.
Selecting the appropriate cable jacket is essential for ensuring that your cables perform reliably in their intended applications. By carefully considering factors such as the approving body, application environment, voltage, temperature, cost, and color, you can choose a jacket that provides the necessary protection and meets all regulatory standards. This proactive approach not only extends the lifespan of the cable but also ensures safety and efficiency in its operation.
Related Resources
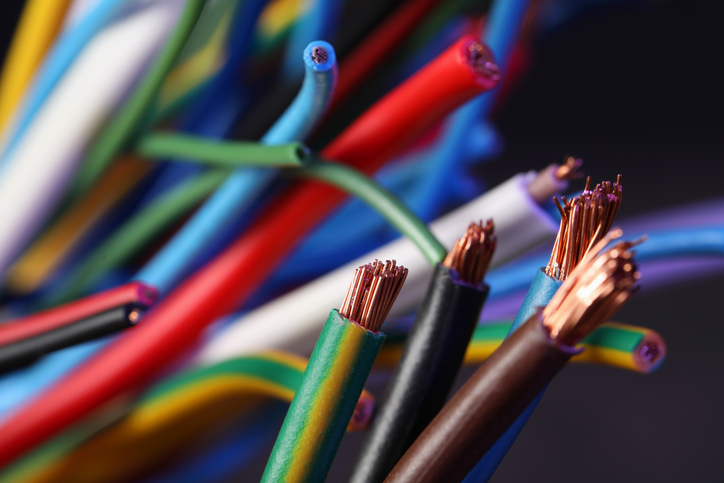
Popular Jacket Types
Jackets cover and protect the enclosed wire or core against damage, chemical attack, fire and other harmful elements which may be present in the operating environment. Learn More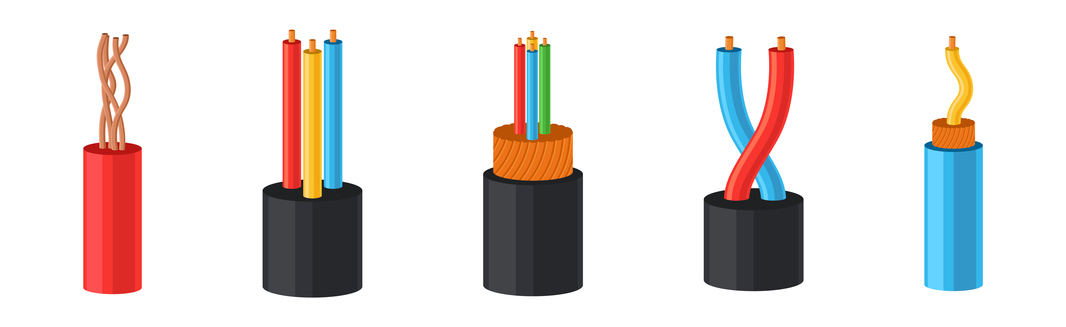
Types of Strand Construction
Strand construction in wire and cable is crucial because it directly affects flexibility, durability, and electrical performance, impacting the overall reliability and efficiency of the cable in various applications.Learn More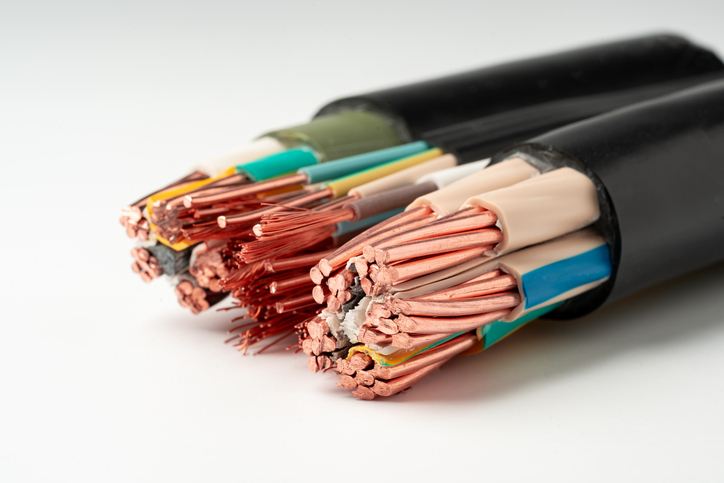
Popular Insulation Types
Insulation is a critical component of any wire conducting an electrical current . The right type of wire insulation is determined by numerous factors, including stability, required life, dielectric properties, temperature and moisture resistance, mechanical strength, and flexibility.Learn More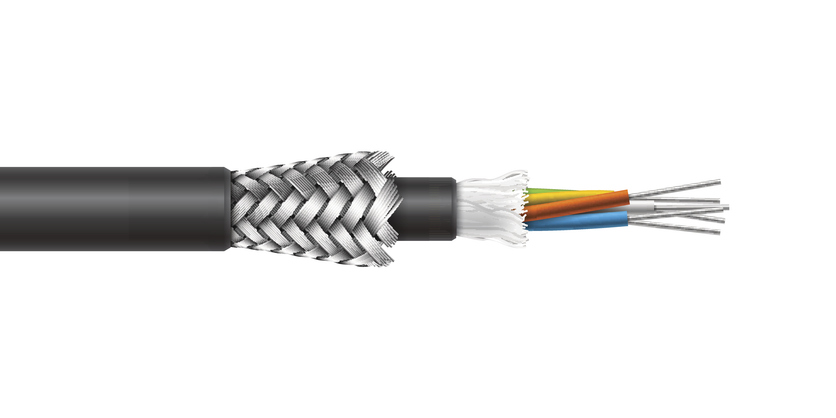