Welding Cable Ampacity & Size Charts
What is Welding Cable Ampacity?
Welding cable ampacity is the maximum current a welding cable can safely carry without overheating or causing damage. This is a crucial factor in making sure that your welding equipment operates efficiently and safely.
The ampacity of a cable determines its ability to handle the high current required by welding machines to generate the necessary arc for welding processes. If a cable is used beyond its rated ampacity, it can lead to excessive heat, potentially damaging the insulation and creating a fire hazard.
An insufficient ampacity can cause voltage drops and reduce the effectiveness of the welding machine, leading to poor welds or equipment malfunction. Understanding ampacity helps you choose the correct cable size to optimize performance and safety in welding applications.
Factors Affecting Welding Cable Ampacity
Several factors impact the ampacity of welding cables and influence their performance and safety. Understanding these factors ensures that the cable you choose can handle the current required by your welding machine while maintaining safe conditions:
- Cable Length: The longer the cable, the more resistance it creates. This resistance can reduce the ampacity and cause a voltage drop, making it essential to compensate for longer cable runs by choosing a thicker gauge cable that can carry the current over the increased distance.
- Cable Gauge: The thickness (or gauge) of the cable directly affects its ampacity. Thicker cables (lower gauge numbers) can carry more current without overheating, while thinner cables have lower ampacity and are better for lighter-duty welding applications.
- Ambient Temperature: The environment the cable is in can also impact its ampacity. In hotter environments, the cable’s ability to combat heat is reduced, meaning the ampacity needs to be reduced to prevent overheating. For example, a cable that works perfectly in a 75°F environment may need a lower ampacity in a 105°F setting.
- Insulation Type: Different insulation materials have varying levels of heat resistance. Cables with high-temperature insulation can handle more current without degrading, allowing for a higher ampacity compared to cables with lower-rated insulation materials. For instance, EPDM rubber insulation is often used in welding cables because of its high resistance to heat and flexibility.
Key Factors for Determining Welding Cable Sizes
- Current-Carrying Capacity (Ampacity): When selecting welding cables, ampacity should be a top consideration. Ampacity is influenced by several factors, such as the length of the circuit, ambient temperature, and duty cycle.
- Circuit Length: The circuit length refers to the total distance the electrical current travels. As the circuit length increases, the potential for voltage drop also increases, meaning that longer circuits typically require larger cables to maintain performance.
- Duty Cycle: The amount of time a welding machine can operate within a 10-minute period without overheating. Duty cycles are crucial in determining the proper cable size since higher duty cycles generate more heat.
View this Page as a PDF >
Required Cable Sizes:
- For Arc Welding Cable Applications
- Length in feet for total circuit* for secondary voltage ONLY
(Do not use this table for 600 volt applications)
Welding Cable Ampacity Chart
Amps | 100' | 150' | 200' | 250' | 300' | 350' | 400' |
---|---|---|---|---|---|---|---|
100 | 4 | 4 | 2 | 2 | 1 | 1/0 | 1/0 |
150 | 4 | 2 | 1 | 1/0 | 2/0 | 3/0 | 3/0 |
200 | 2 | 1 | 1/0 | 2/0 | 3/0 | 4/0 | 4/0 |
250 | 1 | 1/0 | 2/0 | 3/0 | 4/0 | - | - |
300 | 1/0 | 2/0 | 3/0 | 4/0 | - | - | - |
350 | 1/0 | 3/0 | 4/0 | - | - | - | - |
400 | 2/0 | 3/0 | - | - | - | - | - |
450 | 2/0 | 4/0 | - | - | - | - | - |
500 | 3/0 | 4/0 | - | - | - | - | - |
550 | 3/0 | 4/0 | - | - | - | - | - |
600 | 4/0 | - | - | - | - | - | - |
* The total circuit length includes both welding and ground leads (based on 4-volt drop) 60% duty cycle.
Understanding Cable Size Ratings
These values for current-carrying capacity are based on a copper temperature of 60°C (140°F), an ambient temperature of 40°C (104°F), and yield load factor of approximately 32% from the 2 AWG cable, approximately 23% for the 3/0 AWG cable and higher for the smaller sizes.
The sizes of cables generally used ranged from 2 AWG to 3/0 AWG. In actually service, the load factor may be much higher than indicated without overheating the cable as the ambient temperature will generally be substantially lower than 40°C.
Impact of Ambient Temperature and Duty Cycle on Cable Selection
If the ambient temperature is lower than 40°C, you may be able to operate the cable at a higher load factor without causing overheating. The actual ampacity could be higher than the listed values if environmental conditions are favorable. If the ambient temperature rises above 40°C or the duty cycle increases, you may need to choose a larger cable size to handle the increased heat generation.
Suggested Ampacities for 600 Volt In-Line Applications:
AWG | AMPERES | AWG | AMPERES |
---|---|---|---|
4/0 | 315 | 1 | 170 |
3/0 | 275 | 2 | 150 |
2/0 | 235 | 3 | 130 |
1/0 | 200 | 4 | 110 |
- | - | 6 | 85 |
Per standards: ICEA S-19-81
NEMA WC-3 Part 8, Appendix J
Ampacities for portable cable, continuous duty (Ambient Temperature of 40°C)
Proper Cable Selection for Continuous Duty Applications
Proper cable sizing is essential to ensure safety and avoid overheating. Ambient temperatures of 40°C or higher can significantly impact a cable's ampacity, so choosing the right size is crucial for maintaining efficient operations and extending the cable's lifespan.
Choosing the Right Cable for Safe and Efficient Operations
Welding cable selection is an important factor to ensure both the safety and performance in welding applications. By considering the key factors such as ampacity, circuit length, and duty cycle, you can determine the best cable sizes for your needs. Adhering to the recommended ampacity ratings for different AWG sizes is essential to avoid overheating and ensure long-term durability.
Related Resources
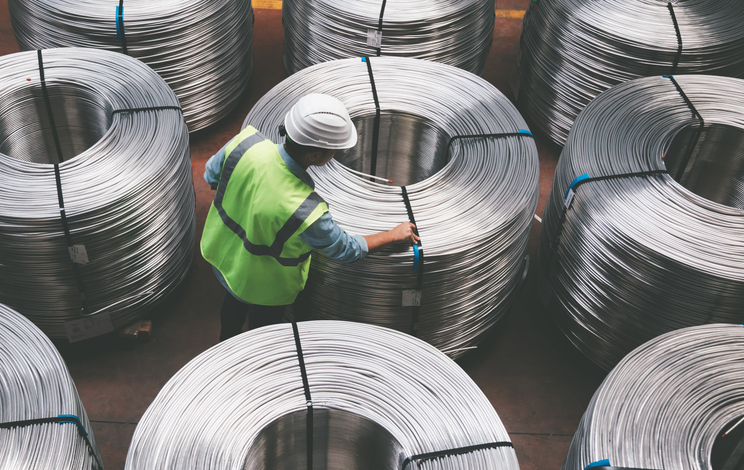
Application & Selection Guide for Standard Product
Read more on the typical applications for standard wire and cable products.Read More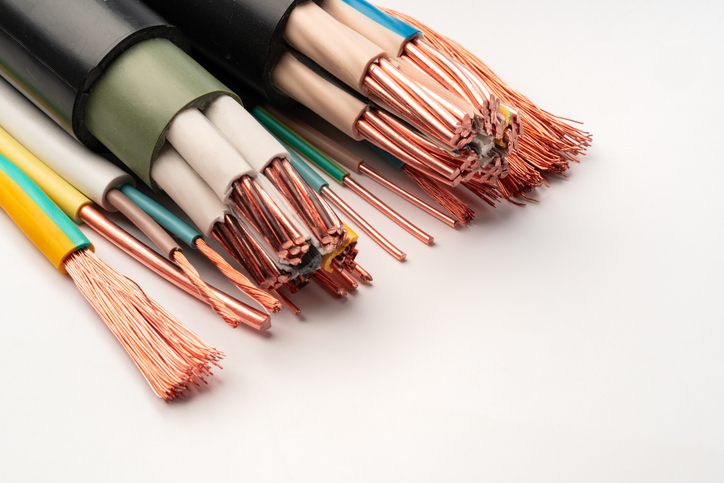
Basic Ampacity Values
Ampacity, or current carrying capacity, is defined as the current a conductor can carry before its temperature rise exceeds a permissible value.Learn More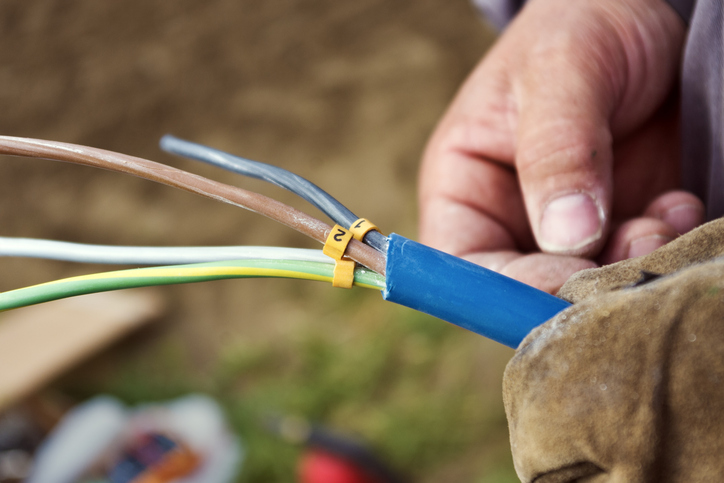
Cable Installation Guidelines
Care must be taken with any flexing application during the installation of the cable. Learn More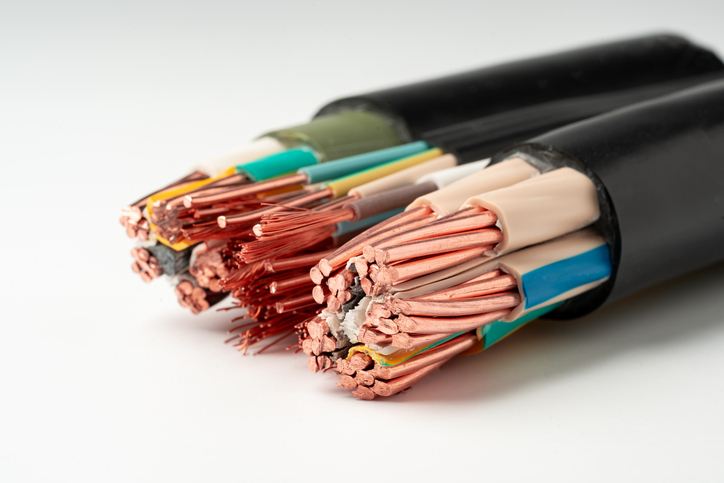